The Digital Twin Revolution in Manufacturing is transforming industries worldwide, bringing efficiency, innovation, and sustainability to the forefront. By integrating virtual models with real-world manufacturing processes, businesses are achieving unprecedented levels of performance and precision. This article delves into how digital twins are reshaping manufacturing, their benefits, and their potential future impact.
What is the Digital Twin Technology?
Digital twin technology involves creating a virtual replica of a physical product, system, or process. These replicas enable real-time monitoring, testing, and optimization of manufacturing systems without disrupting actual operations. This innovation leverages data from sensors, AI, and IoT to simulate and improve processes.
Table of Contents
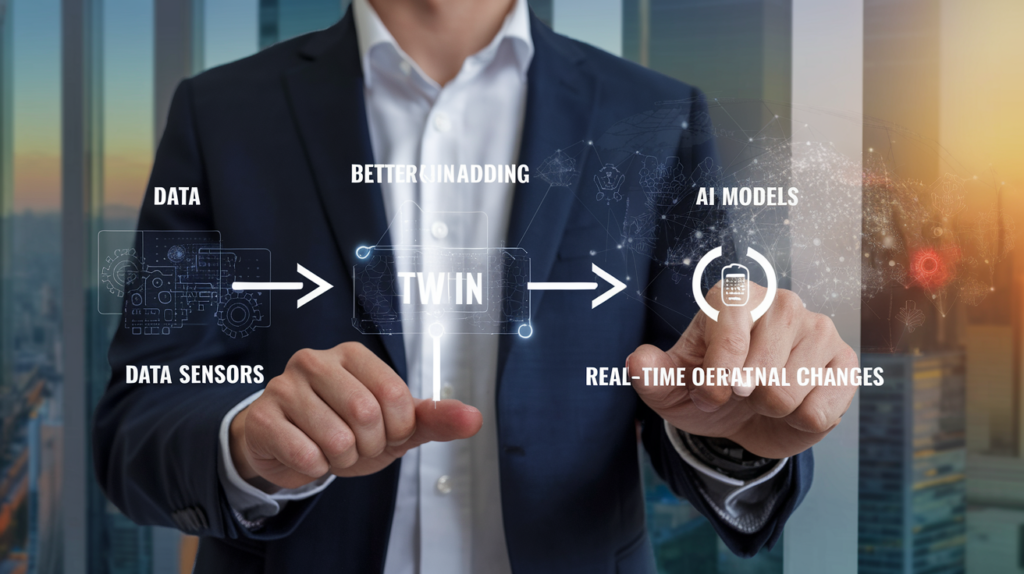
How the Digital Twin Revolution is Impacting Manufacturing
- Enhanced Efficiency:
Digital twins streamline manufacturing by predicting potential failures, optimizing resources, and reducing downtime. This means quicker production cycles and better use of materials. - Improved Product Development:
Virtual simulations allow manufacturers to test designs and make adjustments before physical production, reducing costs and time-to-market. - Sustainability and Waste Reduction:
By optimizing processes, digital twins contribute to lower energy consumption and waste generation, aligning manufacturing practices with environmental goals.
The Digital Twin Revolution in Manufacturing: Key Benefits of Digital Twins in Manufacturing
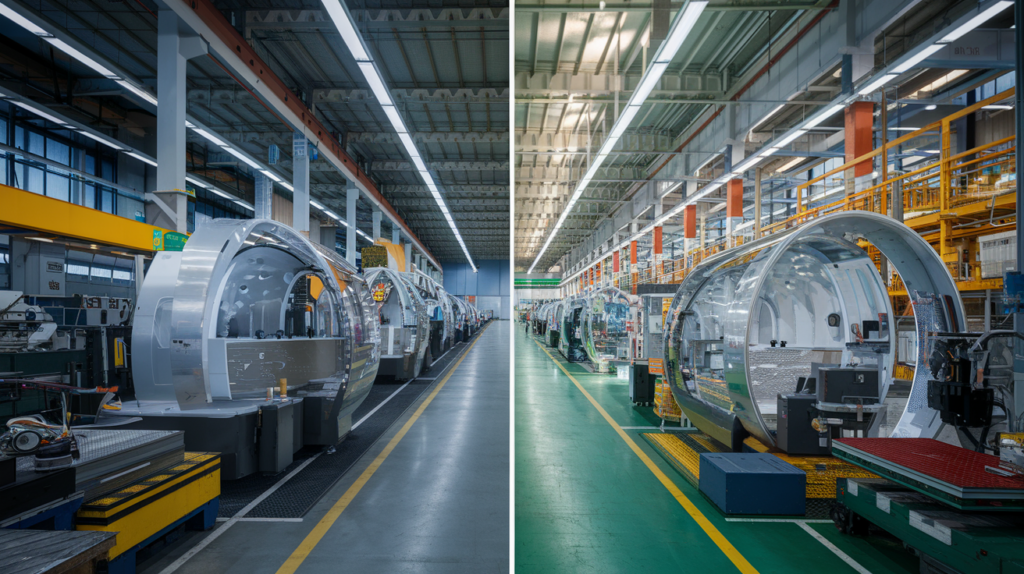
- Predictive Maintenance: Identifying issues before they occur, saving costs on repairs.
- Real-time Analytics: Providing actionable insights to improve decision-making.
- Customization: Enabling manufacturers to design tailored products efficiently.
Future Trends: What’s Next for Digital Twins in Manufacturing?
As the technology evolves, digital twins are expected to integrate more deeply with AI and machine learning. This will further enhance automation, improve accuracy, and open new possibilities for innovation. Businesses investing in digital twins today are positioning themselves for a competitive edge in the future.
Conclusion
The Digital Twin Revolution in Manufacturing is no longer a futuristic concept but a reality shaping industries today. By embracing this technology, manufacturers can achieve significant gains in efficiency, sustainability, and innovation. The integration of digital twins is not just a technological advancement—it’s a necessary step towards the future of manufacturing.
With the right strategy and investment, the potential is limitless. The Digital Twin Revolution in Manufacturing is redefining how industries operate, paving the way for a more efficient, sustainable, and innovative future. By bridging the gap between physical and digital realms, this technology enables manufacturers to optimize processes, reduce costs, and improve product quality like never before. As businesses continue to adopt and innovate with digital twins, they stand to gain a significant competitive edge in an increasingly technology-driven market.
Embracing digital twin technology isn’t just an upgrade—it’s a transformative leap towards smarter, more sustainable manufacturing. The future belongs to those who adapt and innovate, and digital twins are the key to unlocking that future.